Connecting the dots for Optimum Deployment
Diwo unifies and makes sense of multiple complex factors, like the granularity of demand at a location level, and recommends the next best actions. Beyond dashboard explorations that simply pinpoint issues or deliver insights, it presents quantified scenarios that allow the user to add business constraints and layers of context to make distribution decisions at the speed of the Supply Chain.
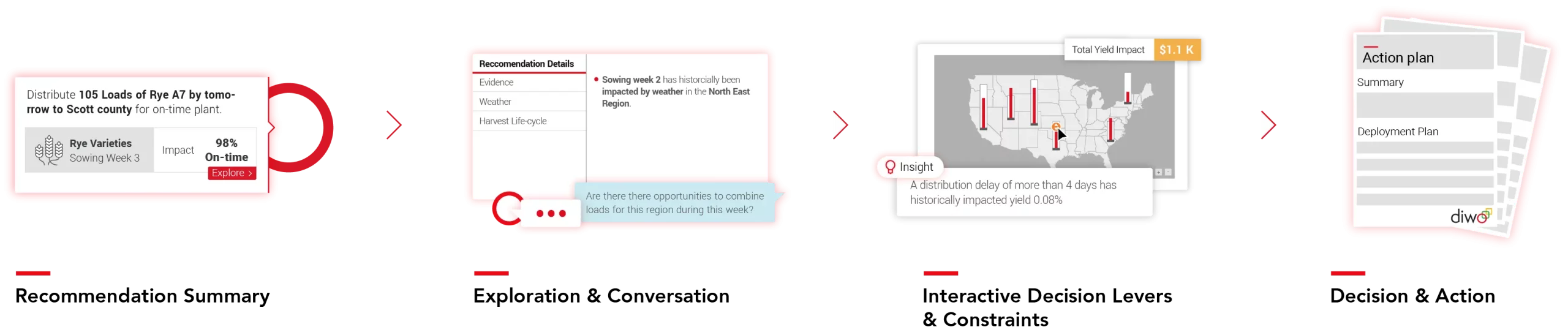
Diwo synthesizes multiple insights with business context to provide quantified recommendations in an interactive, natural language format with business levers and constraints, allowing users to see the impact of their analysis and create an action plan in minutes.
Unlike other Enterprise AI platforms, Diwo’s patented approach to DI focuses on optimizing high-value business decisions, which means time to value is realized much faster and continues to scale across other use cases.
Frequently Asked Questions
Inventory deployment is the process of strategically placing inventory in different locations to meet customer demand while minimizing inventory costs. It involves analyzing demand patterns and transportation logistics to identify optimal inventory levels and locations. Effective inventory deployment requires continuous monitoring and adjustment to ensure optimized inventory levels and locations.